CASE STUDY
CASE STUDY
Plastic to MIM Conversion for Medical Components
APPLICATION
Locking Mechanism for Medication Carts
THE CHALLENGE
A medical device manufacturer needed locking handles for high-end medication carts that were secure, non-magnetic, and corrosion-resistant. The original plastic injection molded components lacked sufficient strength to prevent tampering using low-tech disabling techniques. The geometry required complex, molded features not achievable through traditional machining.
THE SOLUTION
We successfully converted the lock handle components from plastic injection molding to metal injection molding (MIM) using MPP's Conversioneering® process. The transition to MIM-316L stainless steel provided the strength, corrosion resistance, and non-magnetic properties required for the application. Two handle designs were optimized for MIM processing:
Handle 1:
Final weight: 92 grams
Required sintering supports to prevent distortion during processing
Internal diameter extended to reduce cross-sectional thickness
Handle 2:
Final weight: 47 grams
Incorporated lightening features in tool open/close directions to reduce material use
Both handles required coining to restore interrupted diameters that naturally close during sintering
Metal Injection Molding (MIM) enabled us to preserve the original design intent while improving structural integrity and material performance.
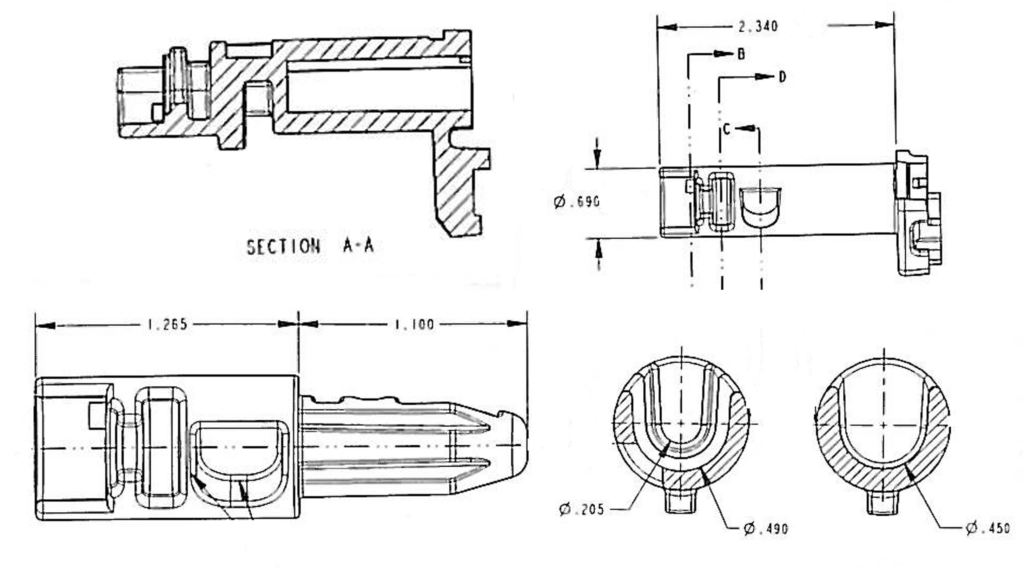
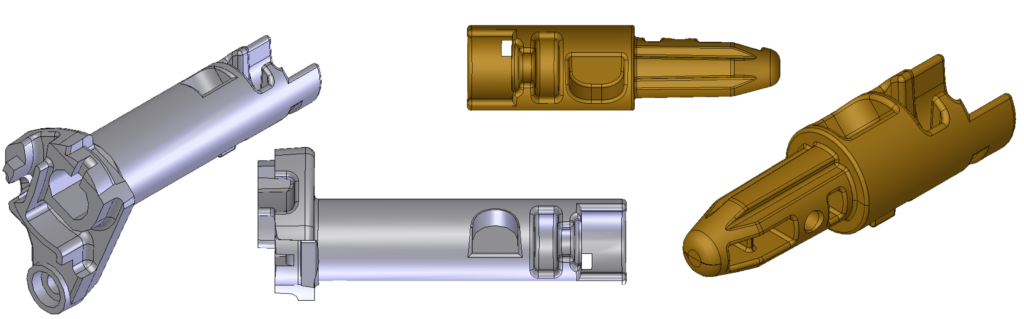
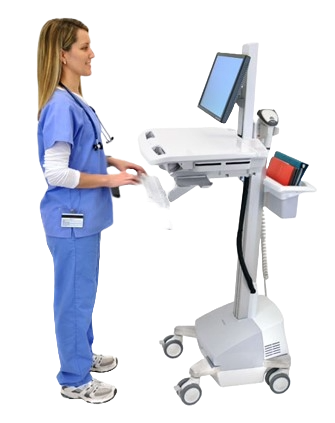
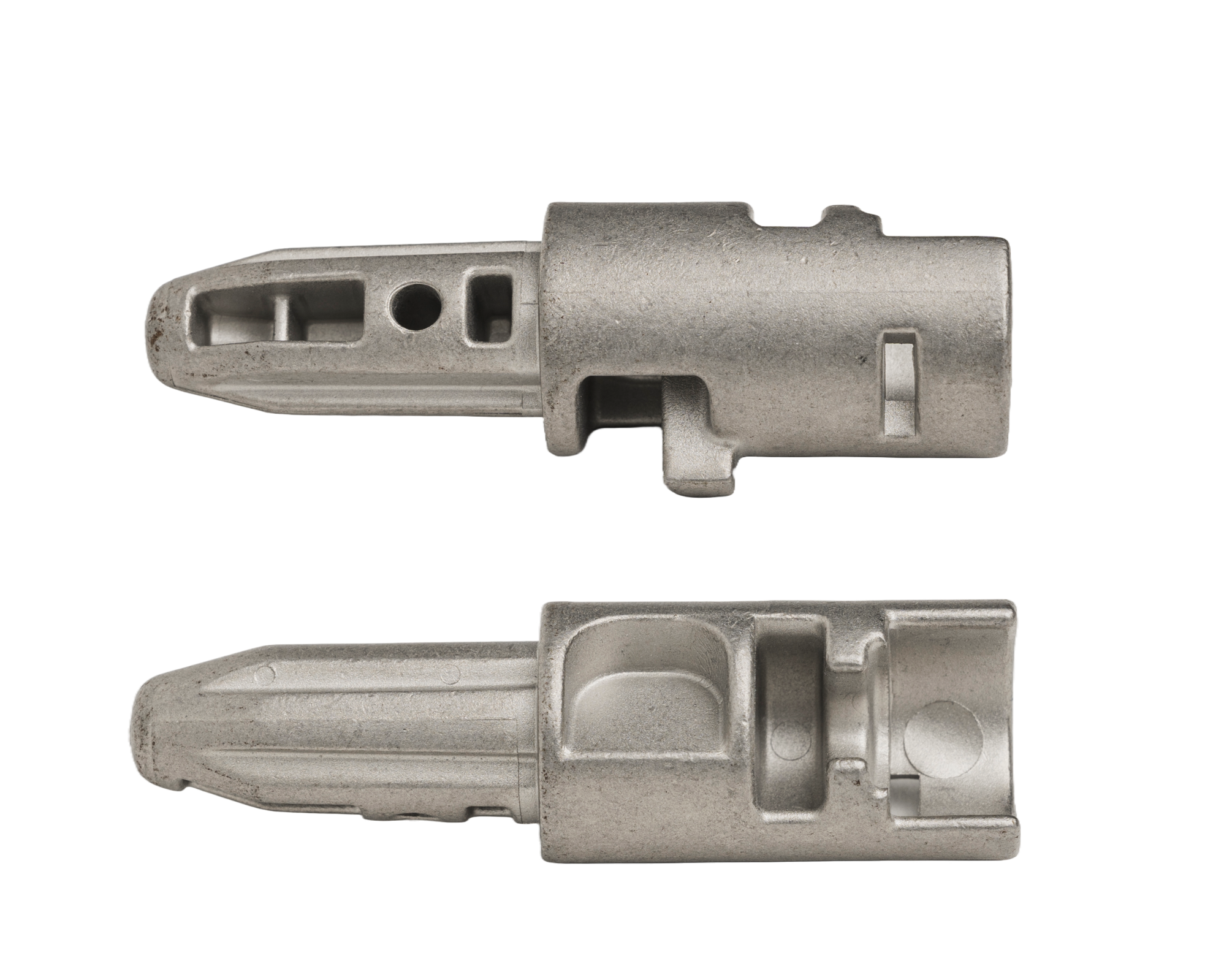
THE IMPACT
By converting the lock handle components from plastic to metal injection molding (MIM), the customer achieved a significant improvement in performance, strength, and reliability. The redesigned MIM parts maintained the original geometry while delivering enhanced functionality critical to secure medical equipment.
Key outcomes included:
Increased part strength with MIM-316L, effectively preventing tampering and low-tech disabling techniques
Superior corrosion resistance, making the components ideal for hospital environments and sterilization processes
Weight optimization through cored and lightening features, maintaining performance without excess material
Precision and consistency enabled by MIM and supported by coining for tight dimensional control
Successful conversion from plastic to metal without redesigning the entire part—retaining complex molded geometries
PARTNERS IN INNOVATION
New Component Design and Conversioneering
Whether you’re interested in designing a new part, converting your components to powder metal, or looking to improve the performance of your current designs you’ll go through a hands on process – from initial conception to completed design. By involving the MPP team as an extension of your engineering department early in the development process, you’re guaranteed maximum value and robust solutions.
Want to learn more about how powder metallurgy works?