Revolutionizing Manufacturing with Powder Metallurgy
Overcoming Production Complexities with Powder Metallurgy
Are you struggling with the challenges of balancing design complexity, precision, and cost in component manufacturing? Traditional methods like casting, milling, and grinding may not meet these demands efficiently, often resulting in increased costs and production inefficiencies. MPP's Custom Powder Metal Solutions provide a superior alternative, optimizing the production process without compromising quality, particularly beneficial in high-volume production scenarios.
Why Powder Metal Stands Out:
Net Shape Capability: Reduces or eliminates the need for additional machining, minimizing scrap loss and lowering production cost.
Cost-Effective for Complex Shapes: Ideal for manufacturing complex or unique shapes that are not feasible with other metal forming processes.
Superior Finishes and Properties: Achieves excellent surface finishes and tribological properties, enhancing the component's functional lifespan.
Consistent Quality: Maintains high consistency and exacting tolerances from part to part, crucial for industries requiring high reliability.
Sustainable Approach: Supports eco-friendly manufacturing practices by utilizing up to 95% recycled materials and by reducing the carbon footprint by up to 50%, all while decreasing energy consumption and material waste.
Explore how MPP's Powder Metallurgy can address your production challenges, delivering durable, precise components more cost-effectively. With our expertise in Metal Injection Molding Services and Advanced Metallurgical Engineering, MPP provides high-quality, tailored solutions that perfectly align with your specific requirements across various sectors, including Automotive, Medical Equipment, and Off-Highway Vehicles. Discover the benefits of partnering with a leader in the powder metal industry, committed to innovation and environmental sustainability.
Powder Metal Process
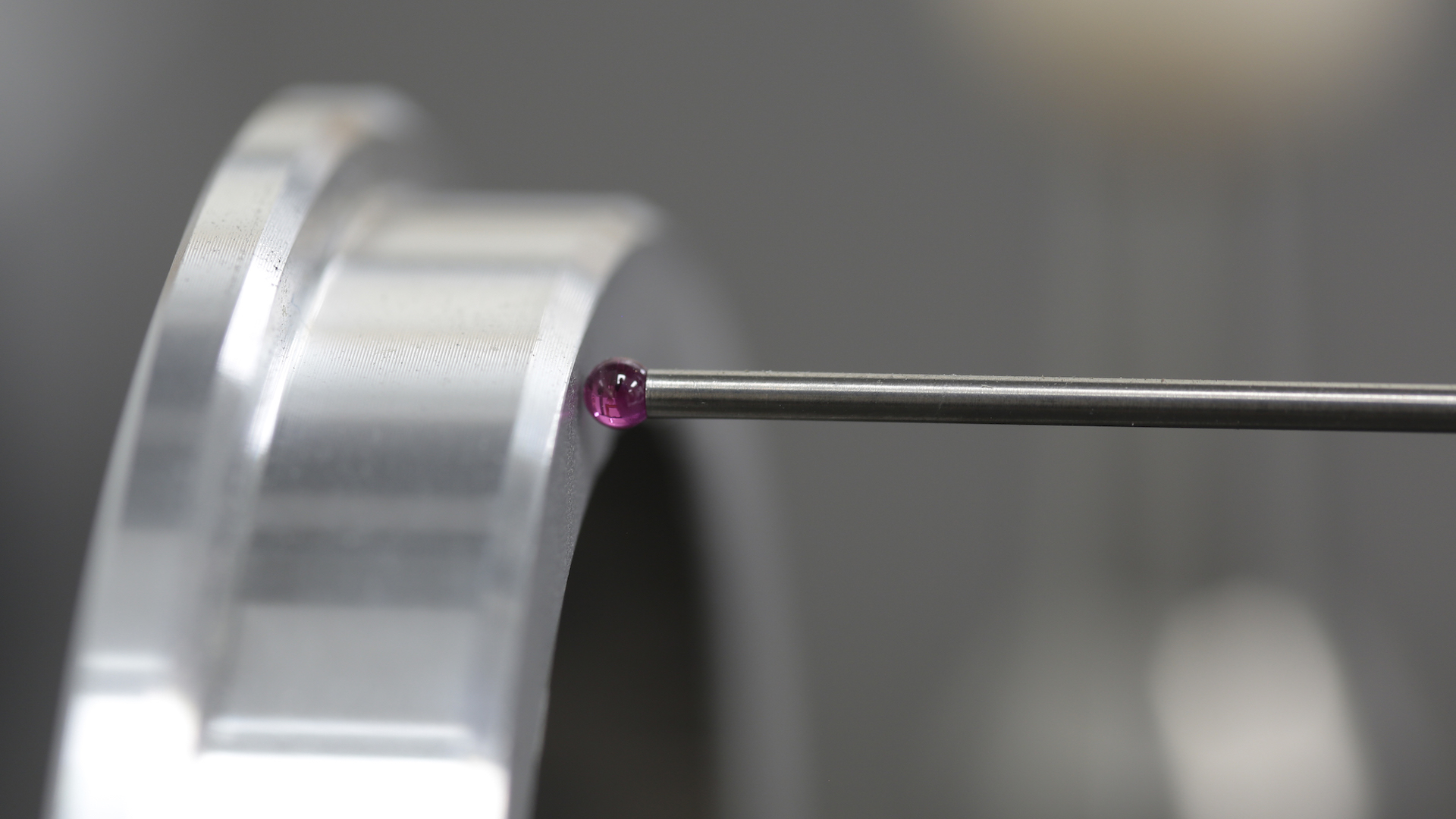
Material Formation
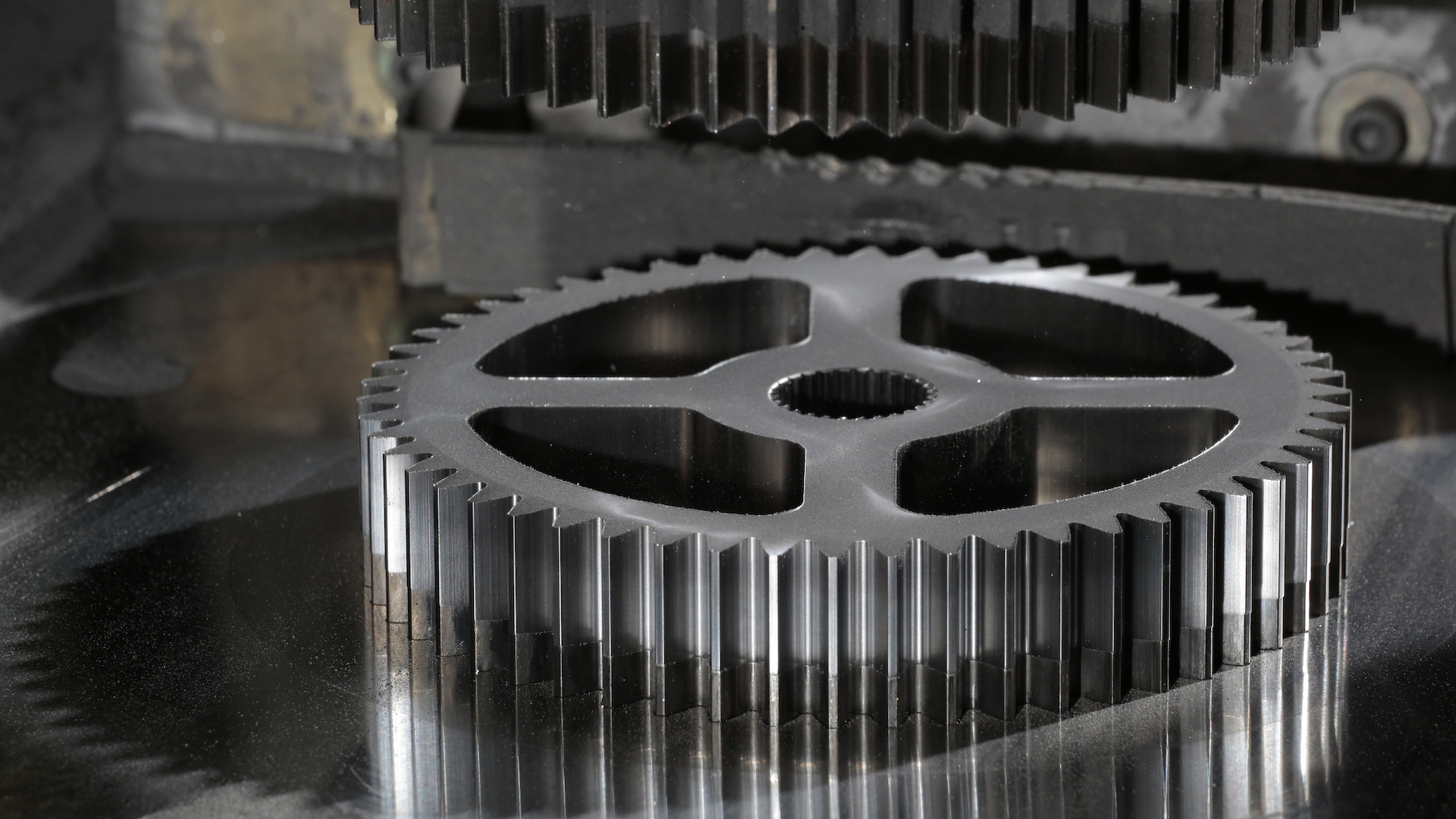
Pressing
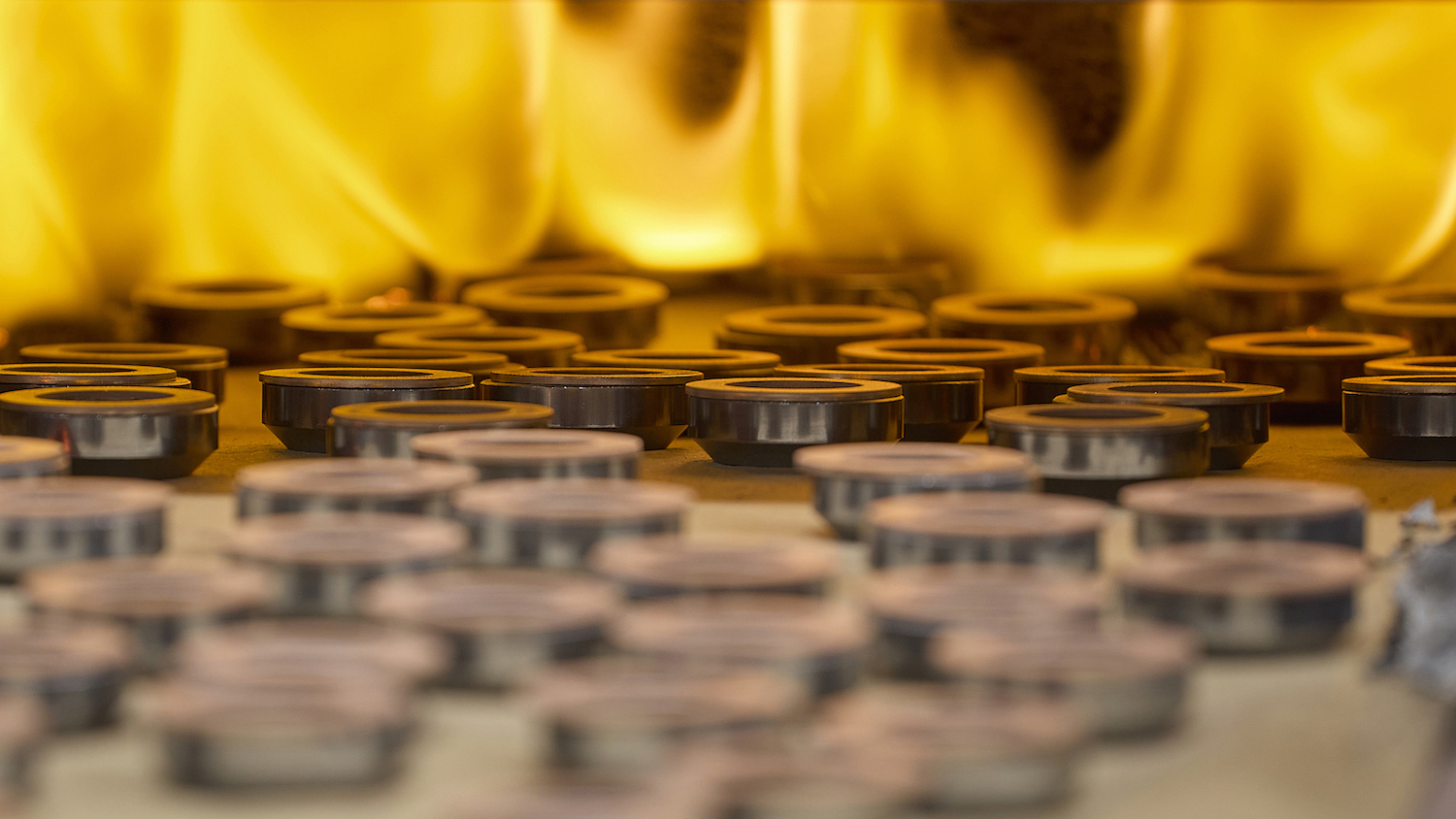
Sintering
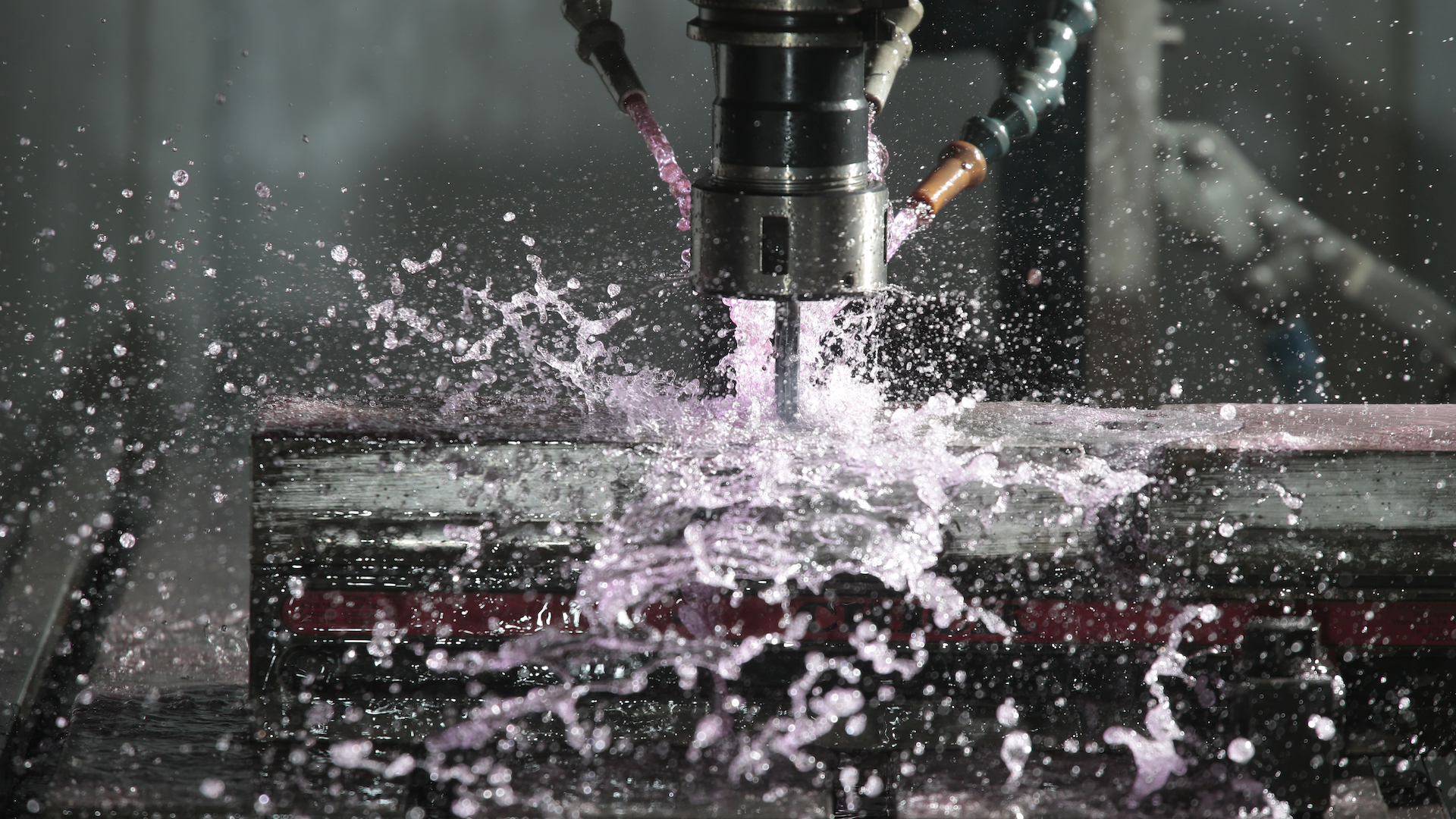
Secondary Operations
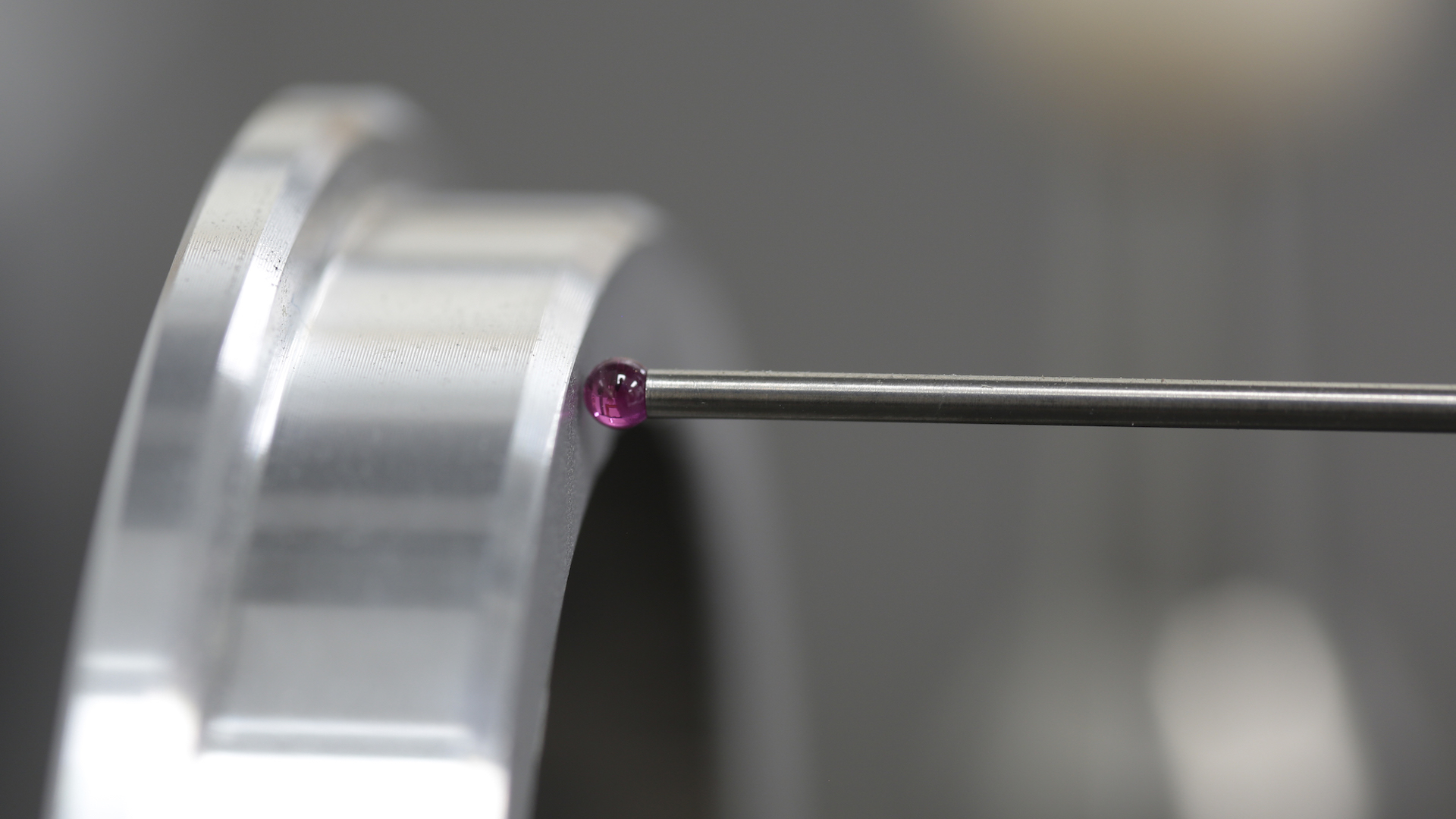
Material Formation
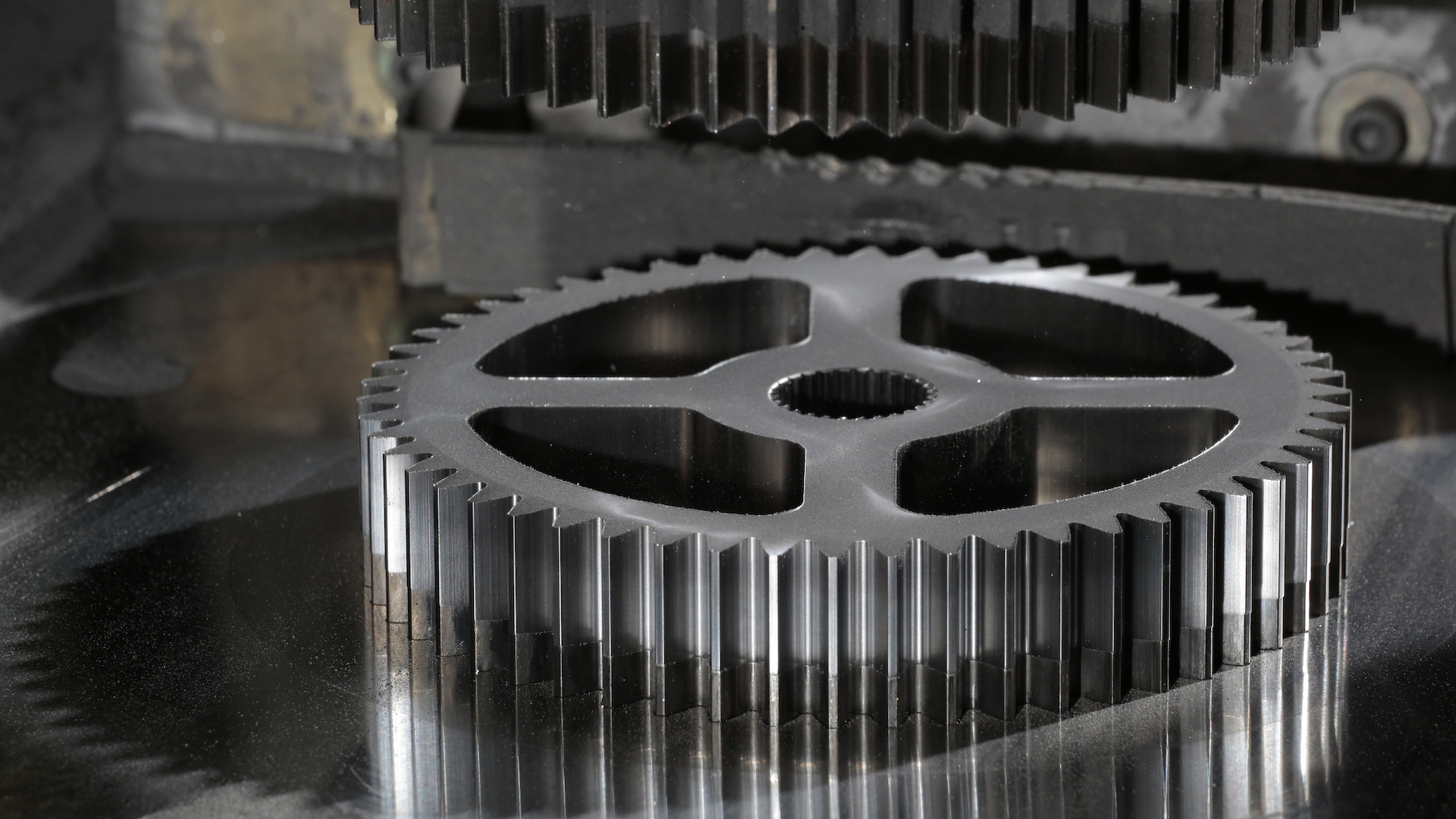
Pressing
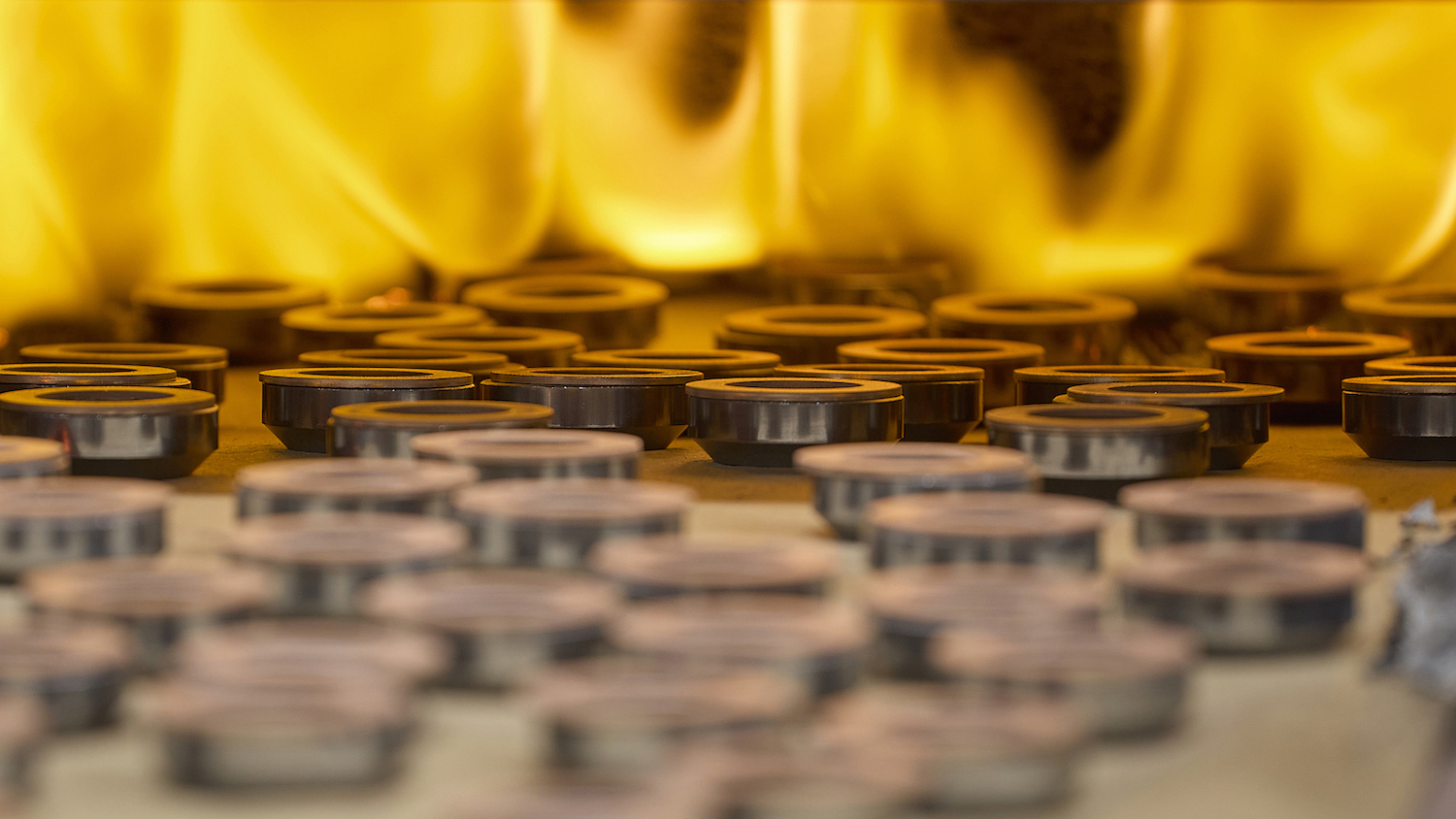
Sintering
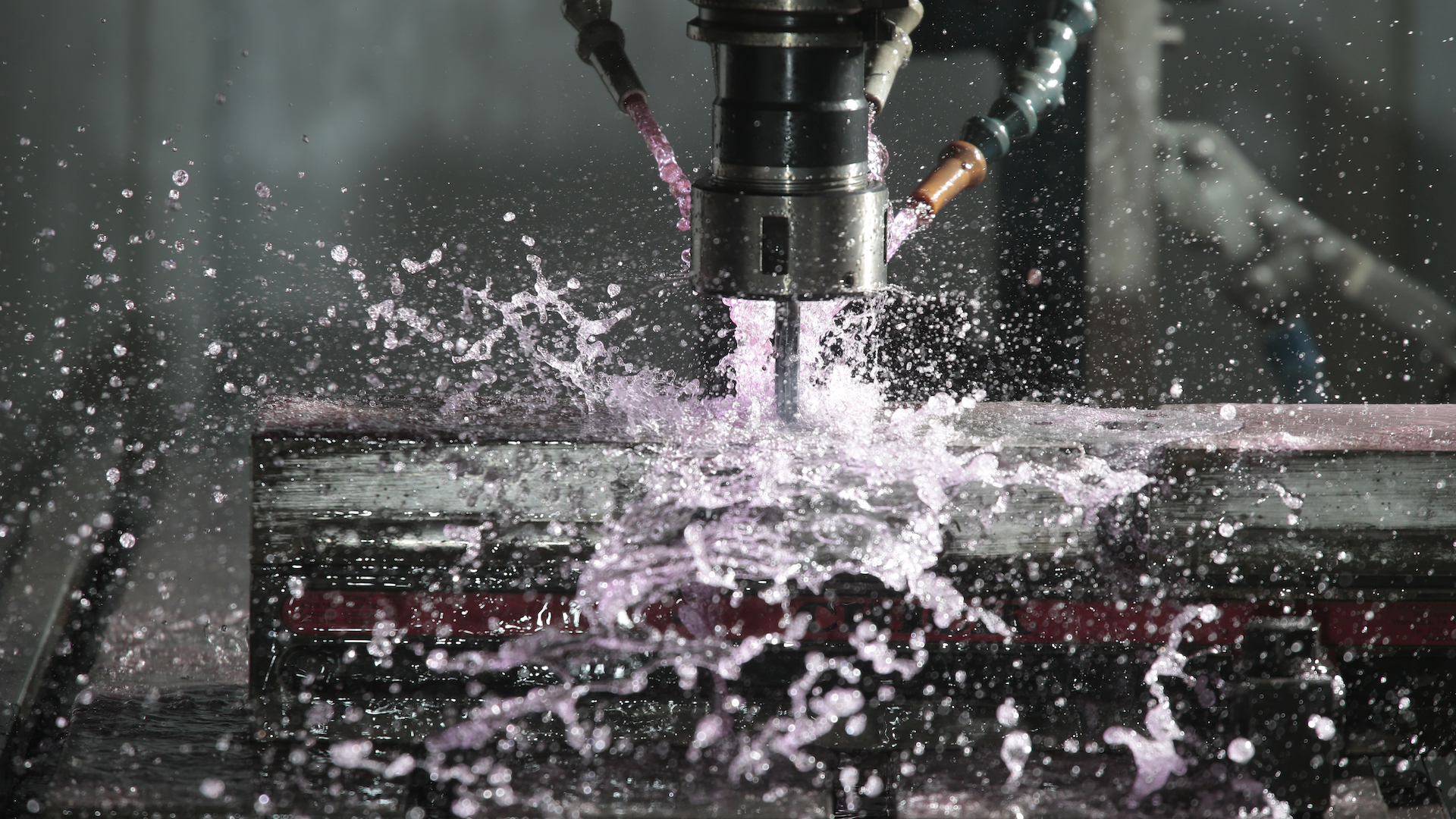
Secondary Operations
Questions about our process?
Optimizing Sustainability with Advanced Powder Metallurgy
Do you face challenges with excessive waste and high energy consumption in your manufacturing operations?
Conventional processes may not adequately address these concerns, impacting both your operational costs and environmental footprint. MPP’s powder metallurgy process confronts these issues directly, efficiently using over 98% of input materials and drastically reducing the energy required for production. Recognized as green technology in metal manufacturing, powder metallurgy not only boosts cost-effectiveness but also significantly diminishes environmental impacts, aligning seamlessly with contemporary sustainability objectives.
Allow our engineers to bring your visionary ideas to life with our advanced metallurgical engineering, perfected over 75 years to adapt and respond to the dynamic demands of our clients.
98% of input material is utilized efficiently, with the remaining excess being recycled and repurposed.
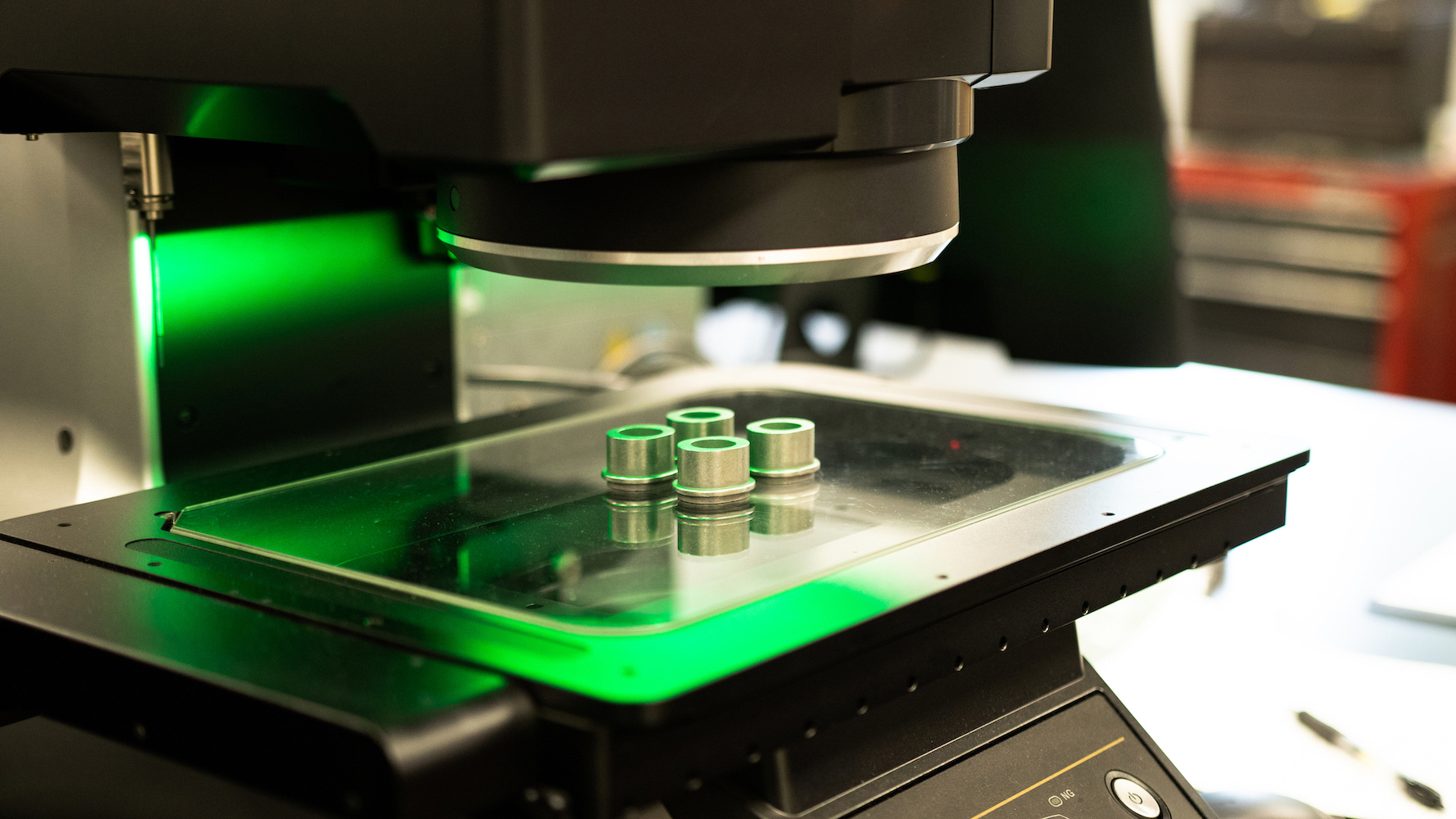
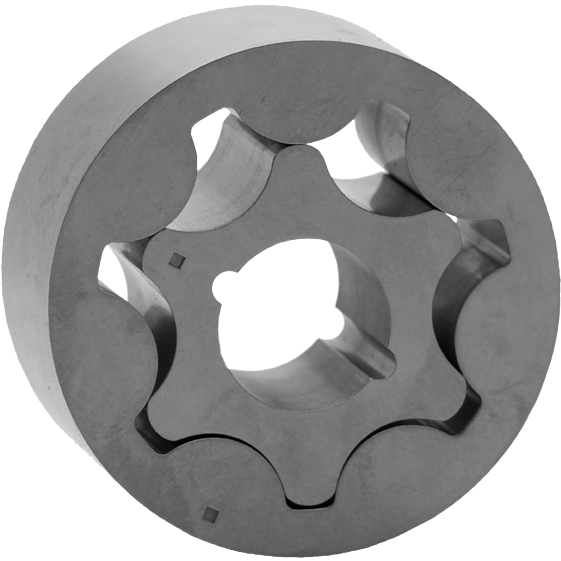
Powder metal components excel in a variety of applications and markets.